- ポール-サイモンは1975年に”あなたの恋人を残す50の方法”という曲を書いたが、プロセス改善を扱うとき、実際には”プロセスを改善する5つの方法”しかない。”それはすべての変化を減らすことについてです; バハマのビストロで顧客にサービスを提供する時間の変化、製品の寸法値の変化–サンドイッチ注文に置かれた肉の量、サービスの品質の変化–メニュー項目 それはすべての変化についてです。
- “5つの道”
- 非付加価値ステップの削減
- 測定システムの改善
- 共通原因変動を減らす
- 特別な原因変動を減らす
- 工程能力を向上させるために平均を移動
- お気に入りの改善方法はありますか? あなた自身が他の人よりも”5つの方法”のいずれかを使用して見つけますか? それについて教えてください!
ポール-サイモンは1975年に”あなたの恋人を残す50の方法”という曲を書いたが、プロセス改善を扱うとき、実際には”プロセスを改善する5つの方法”しかない。”それはすべての変化を減らすことについてです; バハマのビストロで顧客にサービスを提供する時間の変化、製品の寸法値の変化–サンドイッチ注文に置かれた肉の量、サービスの品質の変化–メニュー項目 それはすべての変化についてです。
彼の本では、リーンシックスシグマ技術を使用して組織のための品質管理、博士。 Erick Jonesは、Lean Six Sigmaを”顧客満足度に影響を与え、収益に影響を与えるプロセスバリエーションの削減と画期的な改善の執拗な追求”と定義しています。”私はこの定義が好きです。 それは継続的な旅ではなく、単一のプロジェクトを意味します。 プロセスを改善することは個人的な考え方になります–”これをより良くする方法はありますか?”このプロセスの変化を減らすことは顧客に利点を提供するか。
プロセスを改善することは個人的な考え方になります–”これをより良くする方法はありますか?”
組織内の非常に多くのプロセス、および潜在的な改善を持つそれぞれで、最初のジレンマは、”どこから始めるべきですか?”自分でそれを簡単にします。 あなたが管理または参加しているプロセスを選択し、”どのように私はこれを改善するつもりですか?”現在、私のプロセスにはどのような変化が存在しますか?”
“5つの道”
ここが”5つの道”の出番です。 私の経験では、既存のプロセスを改善する方法は、これらの5つのカテゴリに限定されています:
- 非付加価値ステップの削減
- 測定システムの改善
- 共通原因変動の削減
- 特殊原因変動の削減
- 平均を移動して工程能力を向上させる
重要なのは、どのタイプの改善を努力にもたらしているかを知ることです。 “あなたのプロセスを改善する5つの方法”を明確にしましょう。”
非付加価値ステップの削減
すべてのプロセスは、最初にSIPOCにリストされている一連のステップで構成されています。 しかし、高レベルのビューは、プロセスを真に理解するのに十分ではありません。
最初の要件は、プロセスがどのように動作するかの理解を構築することです。 それがどのように動作すると言われているのか、動作するように文書化されているのかではなく、実際にどのように動作するのか。 “プロセス内の人々は本当に何をしていますか?”プロセスウォークを行うか、プロセス参加者と時間を費やしてプロセスを文書化し、人々(特にプロセス内の人々)が”全体像”を見ることができるようにすると、一般的に簡単に達成可能な結果や迅速な勝利が得られます。
プロセスのボトルネックを探し、ワークロードのバランスをとる方法を模索する。 付加価値のないステップを特定し、それらを排除できるかどうかを判断します。 顧客に利益をもたらす方法で一緒に付加価値のステップをもたらすことができますか? すべてのプロセスには無駄があります。 あなたの仕事はそれを識別し、減らし、また更に除去することである。
次のプロセスを考えてみましょう。 あなたの顧客に500の封筒を組み立て、郵送するために割り当てられる。 あなたは支援するためにボランティアをしている3人の同僚を持っています。 通常、人々はこの活動のための組立ラインに自分自身を整理します,示されているスイムレーンマップと同様.
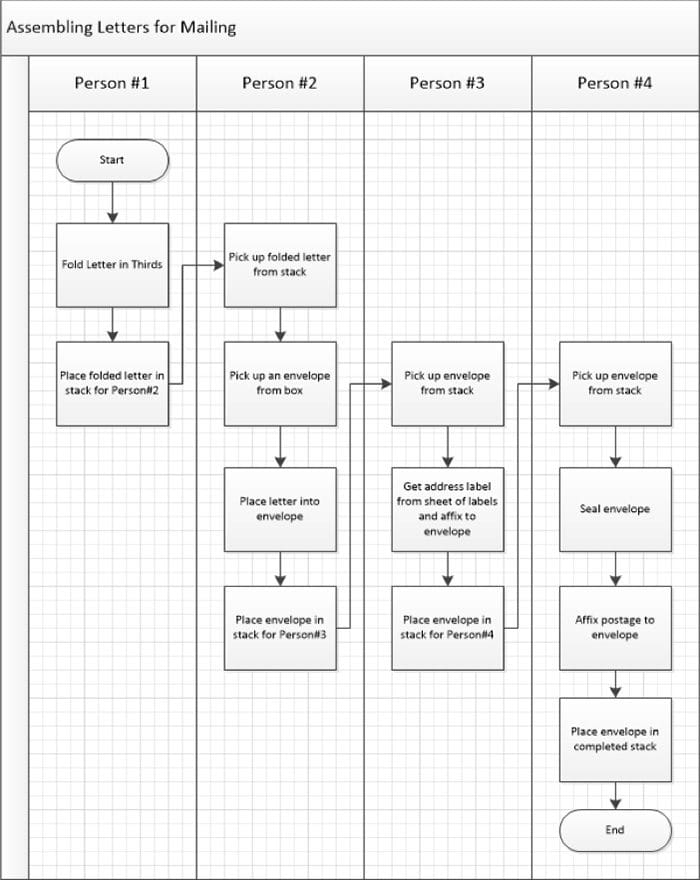
しかし、このプロセスを調べると、付加価値のないステップがいくつかあります。 各スタックとの間のすべての動きは、付加価値ではありません。 なお、折ることはほとんどの時間を取り、従ってプロセスのネックを形作ります。
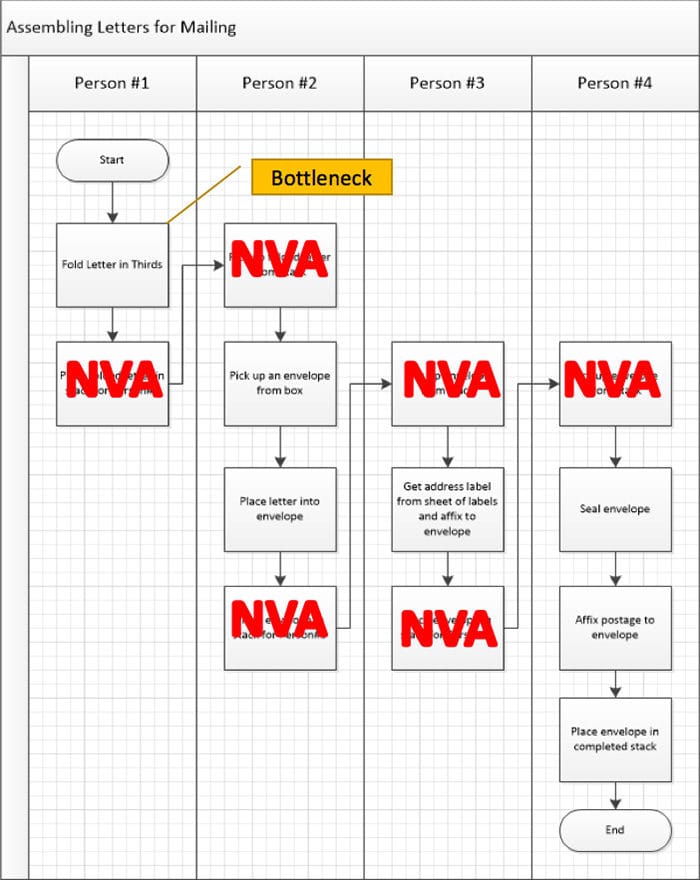
これらの非付加価値のステップを排除することは比較的簡単です。 単に四人のそれぞれが3回それを渡すのではなく、すべてのステップを行う必要があります。 これは、移動のすべてを排除し、アップを拾います。 ボトルネックが4人全員に分散されているため、タスクにかかる時間ははるかに短縮されます。
プロセスの無駄を探してプロセスを簡素化することは、プロセスで作業する人が容易に理解でき、改善を実施するために多くのデータ収集を必要としないため、改善努力を開始するのに適した場所です。
測定システムの改善
データを収集するたびに、観察する変動は、プロセスの変動と測定システムの変動の組み合わせです。
すべての測定システムにはばらつきがありますが、プロセス改善を追求している人は、ばらつきのどれだけが測定されているかの結果であるかを評価することを忘れてしまうことがよくあります。 測定の変動は、各測定の操作定義の明確さにリンクされています。
運用上の定義は完璧ではありません。 測定デバイスがどのように読み取られるか、デバイス上のスケールの有効性、または読み取りが行われた後にオペレータがデータで何をするかにかかわらず、常にいくつかの”解釈”があります。 砂糖の”スプーン”を求めるレシピを考えてみましょう。 それはどのくらいですか–小さじ? 大さじ1杯? 山盛りの大さじ? そこに解釈のための部屋がたくさん。
操作上の定義、この場合は”スプーン一杯”を与えられたときの人々の行動を調べることによって、彼らの解釈の違いを測定することができます。 多くの場合、変動は比較的小さいですが、驚くべきことに、それが大きいときに多くの時間があります。 あなたがチェックしない限り、あなたは知ることはありません。
多くの場合、変動は比較的小さいが、驚くべきことに、それが大きい場合が多い。
私は、多くの企業が測定変動の削減を”有効な”改善プロジェクトとして認識していないのを見てきました。 しかし、変動の減少がリーンシックスシグマの目標である場合、これは確かに法案に適合します。 私は約束します、結果は努力の価値があります。
共通原因変動を減らす
変動はすべてのプロセスに存在するという根本的な原則です。 Walter Shewhart博士とW.Edwards Deming博士は、変化は2つのクラス、一般的な原因と特別な原因に分けることができると支持しました。
これら二つのクラスの分離は、各タイプの変動がプロセスでどのくらいの頻度で観察されるかに関連しています。 一般的な原因の変化は、”定期的に存在しています。”これは、既存のプロセスの一部であり、伝統的に入力(または主要な骨)カテゴリに配置された原因と結果の図(別名フィッシュボーン図)を使用してラベ:
- マンパワー
- 機械
- 方法
- 材料
- 測定
- 環境
この種の変動を減らすには、データを階層化して各要因に起因する変動量を決定する必要があります。 層別要因には、プロセスの場所、早期または後期のシフト、曜日または注文の種類などが含まれます。 アイデアは、これらの要因が存在する場合、プロセス出力に有意な違いを探すことです。
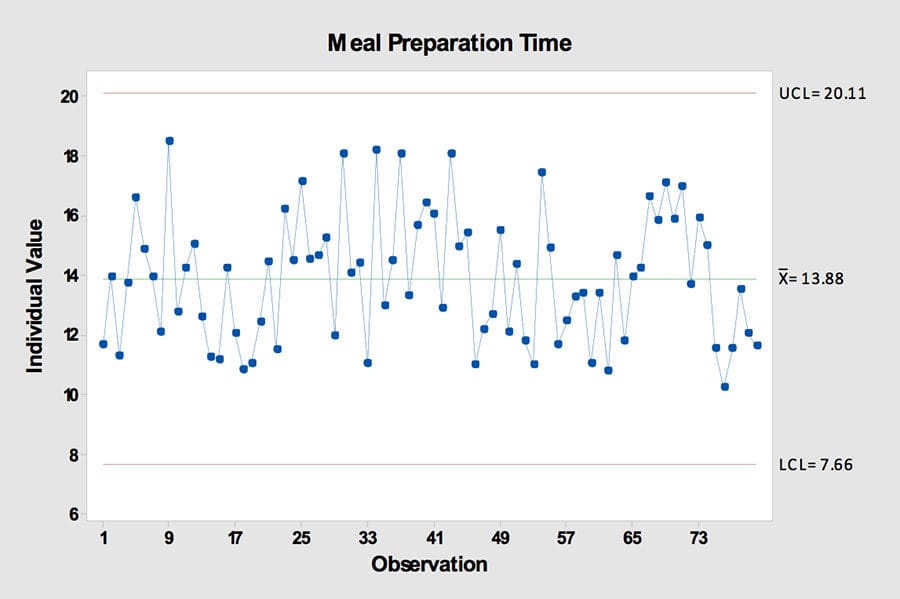
食事の準備プロセスを例にしてみます。 上の管理図は、一般的な原因の変動を示していますが、食事の種類によって層別にすると、データに2つの異なる分布があります。

この違いを知ることは、サンドイッチの準備とは別にサラダの準備の変化を調べるより良い機会を提供します。 サンドイッチは多くの時間がかかるので、それを開始するには良い場所です。
実験の計画はこの情報を収集する一つの方法ですが、受動的に観察するのではなく、プロセスを変更することに積極的に従事する必要があります。
しかし、この情報を入手したら、この変動を減らす方法を追求することができます。 多くの場合、これには、サプライヤーが組織の内部または外部にあるかどうかにかかわらず、プロセスの変動を減らすのを支援するための作業が含 “5つの方法”のうち、一般的な原因の変動を減らすことが最も困難です。
特別な原因変動を減らす
共通の原因変動のみを含むプロセスは、安定または”制御中”とみなされます。”これは、プロセスの変動量が一貫して予測可能であることを意味します。
対照的に、特殊な原因の変動はプロセスを変化させます。 変更は、プロセスにプラスの影響を与える可能性があります、またはそれは否定的である可能性があります。 変更を認識することは、なぜ変更されたのかを理解する機会を提供します。 根本的な原因が理解されれば、情報は顧客に寄与するのに使用することができる。
特殊な原因の変化が含まれています:
- 特定のユニークな変化–吹雪中の交通事故など、管理限界(別名外れ値)外の一点
- 新しい訓練を受けていない料理人がスタッフに追加されたために食重さ

特殊な原因の変動を排除すると、より一貫したプロセスが得られ、全体的に変動が減少します。 重要なのは、いつ変更が発生したかを認識することです。 プロセスの動作/管理図を使用してプロセスを監視すると、これらの変更の警告が表示されます。 これにより、チームは変更が発生した理由を分析することができます。
プロセスの動作/管理図を使用してプロセスを監視すると、これらの変更のアラートが表示されます。
工程能力を向上させるために平均を移動
最初の4つの方法の焦点は変動にありますが、私たちは仕様を必要とする世界に住んでいます。 工程変動は過剰になる可能性があるため、組織は仕様限界を設定して、顧客が経験する変動を狭めます。
仕様に該当するものは”良好”とみなされ、制限を超えたものは再加工または廃棄されます。 プロセスの能力は、仕様内にある出力を提供する能力として定義されます。

変動が大きい場合でも、平均値が二つの仕様内の中心にない場合、一方の値が他方の値よりも多くなるにつれて、リワークの量が大きくなります。 この場合、平均値は55ではなく54.75であり、28%の再作業が発生します。 変動を減少させなくても、平均値を55.0に移動すると、リワークの量が18%に減少します。
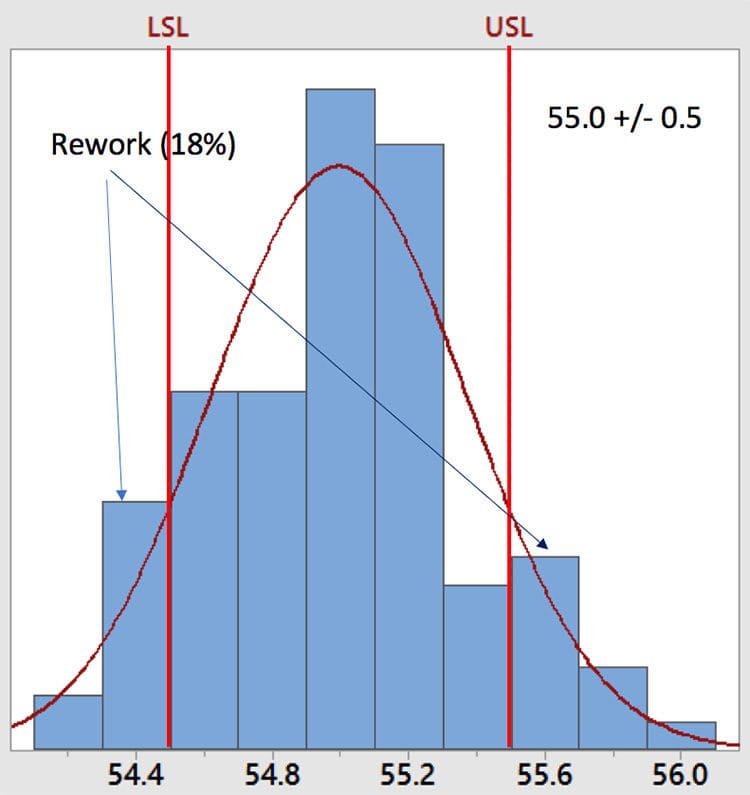
プロセスを改善する際にどの”5つの方法”を使用するかを理解することは、改善努力に焦点を当てるのに役立ちます。 “5つの方法”のいずれかを選択し、最初の改善を行うためにそれを使用して、あなたの改善の努力を開始します。 あなたの成功を祝い、改善が持続できることを確認してから、このプロセスを改善する別の方法を探すか、別のプロセスを選択して作業してくださ それは本当に簡単なことができます!
改善努力は継続的であるべきである–一度に一歩、顧客満足度を向上させ、および/またはボトムラインを増加させるバリエーション削減の執拗な追求。